One of the latest trends in workplace safety is adopting what’s become known as “zero harm culture.” As implied, this new philosophy aims to have absolutely zero accidents that cause injury or fatality in the workplace. Considering that there are more than 14 workplace fatalities per day in the United States, there’s plenty of motivation to strive for a zero harm workplace.
A zero harm workplace embraces the ideology that every employee or visitor should experience a consistently safe work environment. It’s an overarching philosophy that is designed to focus safety decisions entirely on reducing harm, rather than chasing other KPIs that seem to more directly impact your bottom line.
Surprisingly, investing in safety will certainly impact other business metrics in a meaningful way. OSHA estimates that every $1 spent on enhancing employee safety returns approximately $5 back to the business. The key is to continually pursue a zero harm culture by adopting new policies, procedures, and embracing advanced safety software to achieve this important goal.
Today, we’re going to dive deeper into why zero harm culture is worth pursuing, go over some critiques of the movement, and discuss actionable strategies that your company can put to use.
What exactly is the zero harm culture?
Zero harm culture is an overarching ideology that strives to entirely eliminate accidents that cause any level of harm. Unlike some other trends in workplace safety, the term “zero harm” does not necessarily include a set of actionable strategies that must be followed. It’s more of a general emphasis on reaching for an extreme safety goal – to do no harm.
There are plenty of critics of zero harm culture, however. The main criticism of zero harm culture is that it is an unreachable goal that lacks specific direction on how to achieve it. Critics say that setting a company’s safety goals so low without specific guidance is a poor way to manage workplace safety.
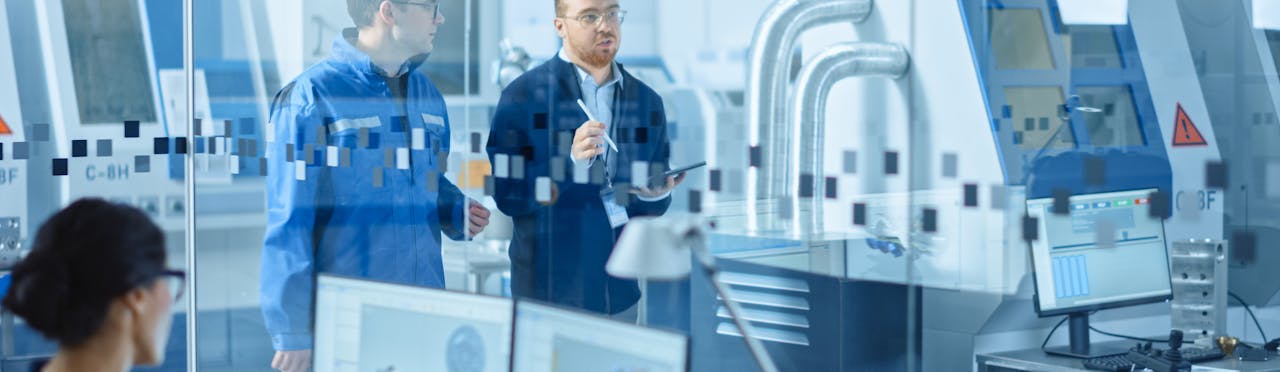
These criticisms may seem valid, but ultimately, they’re missing the entire point of zero harm culture. The goal is to have such a heavy emphasis on workplace safety that you dramatically reduce accidents and continually analyze ways to keep employees safe at work. It’s not necessarily a pie-in-the-sky dream, but a declared company-wide emphasis on workplace safety.
Embracing zero harm culture does not mean that you naively believe that all risks and hazards in your workplace will disappear and you will never have an accident again, as critics of the movement seem to think. Just like pursuing “inbox zero” (the goal of keeping your email inbox empty) doesn’t mean that you’ll never receive another email, zero harm culture means taking every incident seriously and analyzing ways to prevent it from occurring again.
Risks and hazards will still be present, but a zero harm company is well aware of them and has taken every step to minimize them from causing injury. If an incident does occur, it is thoroughly investigated and may result in new policies and procedures.
Actionable strategies to embrace zero harm culture
Since one of the common critiques of zero harm culture is that it lacks specific direction, let’s change that. The way that you enact each of the below actionable strategies will certainly vary based on your company’s exact needs and resources, but they are a great place to start examining your current safety policies and consider making changes.
Create robust safety policies and procedures
Employees are your most important asset, but they also play a vital role in preventing (or creating) accidents that result in an injury.
Safety managers and officers should craft robust safety policies and procedures that are clearly communicated to employees. This is certainly a traditional approach to increasing workplace safety, but it reliably helps reduce incidents.
Ideally, your company will draft enhanced safety protocols after the decision has been made to firmly embrace zero harm culture. Employees should receive in depth training on your new policies.
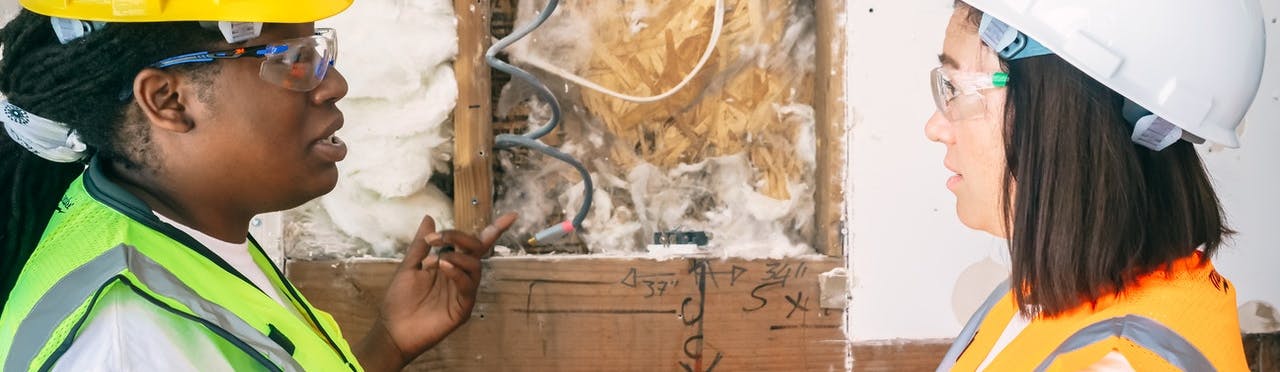
Enact thorough reporting systems
How is your company tracking safety inspections? If you’re still relying on paper checklists, you’re missing out on the ability for managers to track and monitor safety inspections for the entire company.
A comprehensive inspection software solution empowers your workers to thoroughly document and report safety inspections as they go about their daily responsibilities. This strategy is essential for fully embracing zero harm culture since it greatly improves the visibility and transparency of safety inspections.
Rather than a pile of paper checklists collecting dust, inspection software digitizes this vital information that can then be used to inform data-driven decisions and make third-party audits much easier.
Increase your focus on risk management
We know that risks and hazards are not going to disappear from the workplace. Rather than accept injuries as an inevitability, zero harm culture compels you to endless pursue managing the risk present in your facility.
Instead, your company should decide at the highest level that risk management is a key focus of the entire organization. This is what it truly means to embrace zero harm culture – a company-wide focus on eliminating harm.
You need the right tools to adopt zero harm culture
It’s possible that your company already has everything it needs to adopt zero harm culture today and start making meaningful changes. However, it’s more likely that you’ll need to explore new tools to empower your safety managers to make the right decisions.
Inspection and auditing software work to create enhanced transparency, accountability, and data-collection by increasing visibility and awareness around workplace safety.
Are you ready to see how our mobile inspection software can help your company embrace zero harm culture? Start a free monitorQA trial today and discover how intuitive software can make adopting the zero harm culture possible at your workplace.